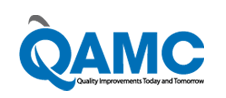


1. Quality has to be defined as conformance to requirements, not as goodness
Management's job is to establish the requirements, supply the wherewithal, and encourage and help employees to get the job done. The basis of this policy is DRIFT - "Do It Right The First Time". Requirements for quality must be thoroughly understood and accepted.

2. The system for causing quality is prevention, not appraisal.
The first step toward defeat and error prevention is to understand the process by which the product is produced. When a defect occurs, discovery and elimination is top priority. Prevention is a knowledge issue for quality-focused workers.

3. The performance standard must be zero defects, not "that's close enough".
The only performance standard that makes sense for DRIFT is zero defects. Zero defects needs to be a performance standard for everyone in the company, from top management to workers on the line.

4. The measurement of quality is the price of nonconformance, not indexes.
A dollar figure can be established for the cost of quality by determining the difference between the price of nonconformance (PONC) and the price of conformance (POC). PONC is the expense of doing things the wrong way and can account for 20% to 35% of revenues. POC is the expense of doing things right - typically 3% to 4%. COQ is not a standard to be met. Rather, it is a flow. Managers should spend time identifying where it is occurring and address what makes it occur.
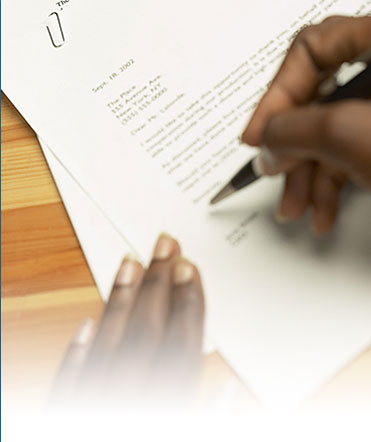